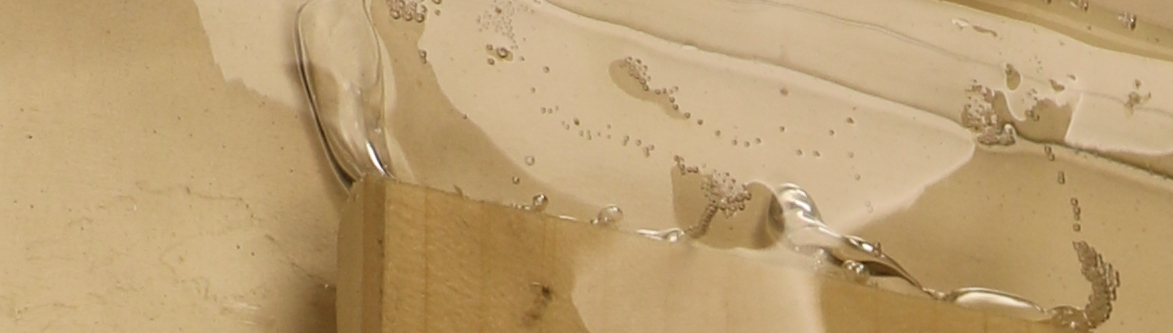
Causes and possible solutions for air bubbles in epoxy resin castings
In this article, we focus on the air bubbles that form during the hardening of our medium and high thickness epoxy resins.
First of all, it is necessary to understand that air bubbles cannot be completely removed. If the requirement is to always obtain a finished surface without any bubbles and with materials encased, this is almost impossible.
Bubbles are like dust on lacquered wood, no matter how hard you try to avoid them, the surface is always affected.
We want to point out first that large castings for table product requires experience and testing. It is not realistic to think that anyone can make a table out of resin and wood without having any experience. Yoy can see this process in many videos on the internet where the operation seems simple and feasible by anyone.
Air bubbles in epoxy resins are mainly divided into 2 categories:
- Bubbles caused by inadequate insulation of the substrate or incased material
- Unforseen bubbles that are found at the end of a “skillfully executed” application
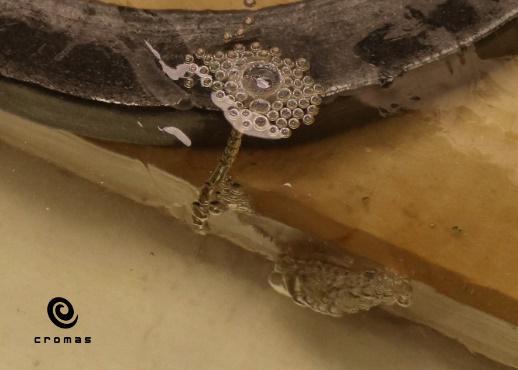
Epoxy resin bubbles from non-insulated surfaces
Epoxy resin bubbles from non-insulated surfaces, they occur during hardening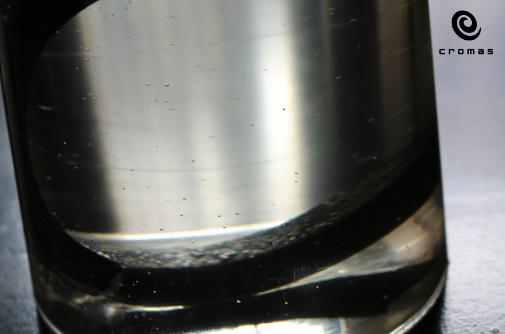
High thickness epoxy resin bubbles
High thickness epoxy resin bubbles occurred during hardeningThe bubbles from a not well insulated material can be avoided with sealing agents and thixotropic resins as long as the materials are not sponge-like. If they are sponge like, we suggest to change the material to have good results.
The unforseen bubbles, on the other hand, are bubbles that appear, even with low exothermic resins (low heat curing rise), once the hardening has been completed or started. This is the most common in craft and industrial processing, and occurs mainly with encased woods.
The causes of the bubbles are mostly environmental and sometimes it is the surface tension between the resin and the mold. It must be noted that the epoxy resin does not develop GAS during curing with the amines that serve as a hardener.
The bubbles are not caused by the resin, but by the expansion or release of gas from the environment, the inserted materials or the mold during curing.
It is no coincidence that problems occur during the cold season, especially in winter. During these periods, the resin is more viscous, the release of gases or vapours is slower as well as the release of dissolved gases into the resin during mixing and casting. In addition to this, hardening is slower.
The most effective solutions to reduce bubbles:
- Heat up the resin and if possible heat up the mold before casting and during the first casting phase
- Avoid a drop in ambient temperature, it is no coincidence that in the summer it is warmer in the factory buildings and the casting of the resin is perfect
- Use a heat gun while making the casting
- Build the thick casting in several close layers, always passing the heat gun over the resin and, if possible, over the edges of the mold
- Always work and store the material in a dry and not humid environment
The most effective solution, but also more complex is the vacuum casting mold.
- Make the casting with a vacuum pump or a vacuum casting of the mold. This is the most effective method to reduce the formation of bubbles and is a common industrial practice in the production of objects in plexiglass and polycarbonate, a process similar to epoxy resins.
Are there more direct and simple solutions? Yes
The simplest and most convenient industrial solution is to change the process versus complete transparency, for example:
- Colour the resin, at least partially, so that bubbles are hidden. This colouring can be either semi-transparent or opaque. In most of the videos and articles on the internet, they always show a coloured resin so they can hide the bubbles.
- Use the three-dimensional epoxy resin in combination with special paint effects. In this way, you can work with low thickness epoxy resins over the finished special paint effects and this will make it difficult to see any bubbles.
- Make multiple low thickness castings. With a low thickness epoxy resin castings, less than 10 mm, the formation of bubbles are more controllable becaue they have a shorter distance to exit the resin. With the use of the heat gun, it is also possible to make them come out more quickly. When multiple layers are applied and cured, you will see the different layers of the resin, as if they were laminated glass.
Cromas has invested a lot of time and resources in the development of these products, the main resins for professional use developed are:
- transparent epoxy resin for casting for low thicknesses
- transparent epoxy resin for thicknesses from 1 to 3 cm approximately, with small englobes
- transparent epoxy resin for high thicknesses (even over 20cm) with englobes
All this information was based on our extensive research and experience to help you with your production tests and to solve problems that may occur during the application process.